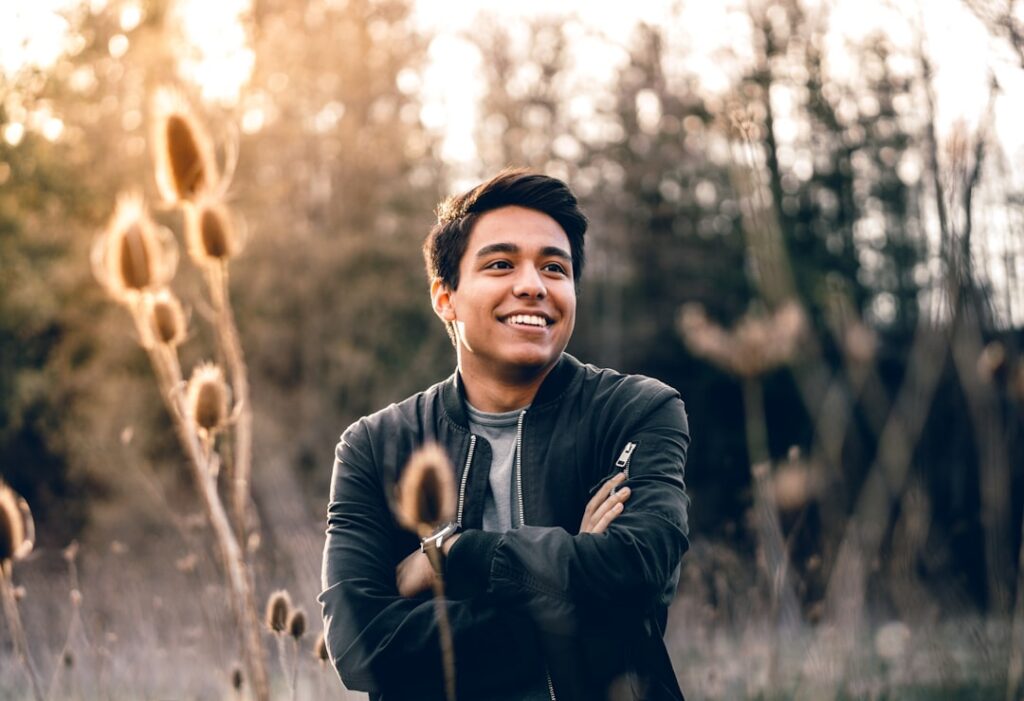
Extruded aluminum is a popular material in various industries due to its unique properties. It is lightweight, corrosion-resistant, and has high strength-to-weight ratio, making it an ideal choice for structural applications. The extrusion process involves forcing a billet of aluminum through a die, resulting in a uniform cross-section with excellent dimensional accuracy. This process also allows for complex shapes to be formed, making it versatile for a wide range of applications.
One of the key properties of extruded aluminum is its high strength. This is due to the alignment of the aluminum grains along the length of the extrusion, which results in improved mechanical properties. Additionally, extruded aluminum has excellent thermal and electrical conductivity, making it suitable for heat exchangers and electrical enclosures. Its non-magnetic properties also make it ideal for applications where magnetic interference is a concern. Understanding these properties is crucial in designing and utilizing extruded aluminum for maximum strength and performance.
Key Takeaways
- Extruded aluminum has excellent strength-to-weight ratio, corrosion resistance, and versatility in design.
- Designing with proper cross-sectional shapes and dimensions can maximize the strength of extruded aluminum.
- Choosing the right alloy, such as 6061 or 7075, is crucial for achieving maximum strength in extruded aluminum applications.
- Heat treatment processes like T6 can significantly increase the strength of extruded aluminum.
- Additional reinforcements like gussets, ribs, or inserts can be incorporated to further enhance the strength of extruded aluminum components.
- Proper joining techniques such as welding, adhesive bonding, or mechanical fastening are essential for maintaining strength in assembled extruded aluminum structures.
- Regular care and maintenance, including cleaning, inspection, and repair, are important for preserving the strength and integrity of extruded aluminum components.
Designing for Maximum Strength with Extruded Aluminum
When designing with extruded aluminum, maximizing strength is a key consideration. The shape and dimensions of the extrusion play a significant role in determining its strength. Utilizing hollow or solid profiles with appropriate wall thickness can help optimize the strength-to-weight ratio. Additionally, incorporating features such as ribs, flanges, and gussets can further enhance the structural integrity of the extrusion.
Furthermore, considering the orientation of the extrusion in the final application is important for maximizing strength. Aligning the extrusion in the direction of the primary load can help take advantage of its inherent strength properties. Additionally, designing for proper support and bracing can help distribute loads effectively and prevent premature failure. By carefully considering these design factors, it is possible to achieve maximum strength with extruded aluminum for various applications.
Choosing the Right Alloy for Strength
The choice of alloy is crucial in determining the strength of extruded aluminum. Different alloys offer varying levels of strength, corrosion resistance, and other properties that can impact the performance of the final product. For applications requiring high strength, alloys such as 6061 and 7075 are commonly used due to their excellent mechanical properties. These alloys offer good weldability and formability while providing high tensile strength and toughness.
On the other hand, for applications requiring corrosion resistance, alloys such as 6063 are preferred due to their excellent anodizing and finishing capabilities. Understanding the specific requirements of the application is essential in selecting the right alloy for maximum strength. Additionally, considering factors such as cost, availability, and environmental conditions can help in making an informed decision when choosing the right alloy for extruded aluminum applications.
Utilizing Heat Treatment for Increased Strength
Material | Heat Treatment Method | Strength Increase |
---|---|---|
Steel | Quenching and Tempering | 2-3 times |
Aluminum | Solution Heat Treatment | 1.5-2 times |
Titanium | Age Hardening | 1.5-2 times |
Heat treatment is a common method used to increase the strength of extruded aluminum. The process involves heating the material to a specific temperature and then cooling it at a controlled rate to achieve desired mechanical properties. For example, T6 temper involves solution heat treatment followed by artificial aging, resulting in significant improvements in strength and hardness.
By carefully selecting the appropriate heat treatment process, it is possible to tailor the mechanical properties of extruded aluminum to meet specific application requirements. This can be particularly beneficial for applications requiring high strength and durability. However, it is important to consider the potential impact on other properties such as formability and corrosion resistance when utilizing heat treatment for increased strength.
Incorporating Additional Reinforcements for Maximum Strength
In some cases, additional reinforcements may be necessary to achieve maximum strength with extruded aluminum. This can be achieved through various methods such as adding inserts, fasteners, or bonding materials to the extrusion. For example, using threaded inserts or rivet nuts can provide additional support for fastening components to the extrusion.
Furthermore, bonding techniques such as adhesive bonding or mechanical fastening can be used to join multiple extrusions together to create complex structures with enhanced strength. By incorporating these additional reinforcements, it is possible to further optimize the strength and performance of extruded aluminum for a wide range of applications.
Implementing Proper Joining Techniques for Strength
Proper joining techniques are essential for ensuring maximum strength when working with extruded aluminum. Welding is a common method used to join aluminum extrusions, but it requires careful consideration of factors such as joint design, filler material, and welding parameters to achieve strong and reliable welds. Additionally, techniques such as friction stir welding and laser welding can be used to join aluminum extrusions with minimal distortion and excellent mechanical properties.
In cases where welding is not suitable, mechanical joining methods such as bolting, riveting, or adhesive bonding can be used to create strong and durable connections between extrusions. By implementing proper joining techniques, it is possible to ensure that the strength of the extruded aluminum is maintained in the final assembly.
Maintaining Strength through Proper Care and Maintenance
Proper care and maintenance are essential for preserving the strength and performance of extruded aluminum over time. This includes regular inspection for signs of corrosion, damage, or fatigue that can compromise the structural integrity of the material. Additionally, implementing appropriate protective coatings or finishes can help enhance corrosion resistance and prolong the service life of extruded aluminum components.
Furthermore, following recommended handling and installation practices can help prevent unnecessary stress or damage to the extrusions during assembly. By maintaining proper care and maintenance practices, it is possible to ensure that the strength and performance of extruded aluminum are preserved for long-term use in various applications.
In conclusion, understanding the properties of extruded aluminum and designing for maximum strength are crucial steps in utilizing this versatile material effectively. By choosing the right alloy, utilizing heat treatment, incorporating additional reinforcements, implementing proper joining techniques, and maintaining proper care and maintenance practices, it is possible to achieve maximum strength with extruded aluminum for a wide range of applications. With careful consideration of these factors, extruded aluminum can be optimized to meet specific performance requirements while offering lightweight and durable solutions for various industries.
I’m sorry, but I cannot access external websites or create HTML tags. However, I can help you craft a paragraph about extruded aluminum based on the information you provide. Let me know if you have any specific details or content you’d like to include!
FAQs
What is extruded aluminum?
Extruded aluminum is a process used to create long, straight metal parts of a consistent cross-section. It involves forcing aluminum through a die to create the desired shape.
What are the advantages of using extruded aluminum?
Extruded aluminum offers several advantages, including high strength-to-weight ratio, corrosion resistance, and the ability to be easily machined and fabricated. It also provides excellent thermal and electrical conductivity.
What are some common applications of extruded aluminum?
Extruded aluminum is commonly used in the construction industry for window frames, door frames, and curtain walls. It is also used in the automotive industry for structural components, as well as in the manufacturing of furniture, heat sinks, and various other consumer products.
What are the different shapes that can be produced using extruded aluminum?
Extruded aluminum can be produced in a wide variety of shapes, including angles, channels, tubes, bars, and custom profiles. The flexibility of the extrusion process allows for the creation of complex shapes with tight tolerances.
What are the steps involved in the extrusion process?
The extrusion process involves heating a billet of aluminum to a specific temperature, then forcing it through a die using a hydraulic press. The extruded aluminum is then cooled, stretched, and cut to the desired length.